Как подобрать установку плазменной резки?
Среди способов раскроя металла самым популярным и экономичным является плазменная резка. Этот способ раскроя подходит большинству видов металла и сплавов и применяется практически во всех областях промышленности, где требуется быстрая и качественная резка металла.
Кроме того данная технология обладает значительным преимуществом по параметру максимальной толщины обработки при резке, по легкости и скорости перенастраивания на конкретную конфигурацию детали, по простоте обучения и подготовки квалифицированного специалиста для работы на ней.
В основе работы плазменных установок заложена простая и удивительная физика – взаимодействие электричества и газа. В станке производится непрерывная подача определенного вида газа в столб дуги, дополнительно сжимаемой вихревым потоком газа. Благодаря этому создаётся источник тепловой энергии. Энергия дуги воздействует на газ, и происходит процесс его ионизации. При этом температура газа повышается, и он превращается в плазменную струю. Этой направленной струей и производится резка металла. При этом скорость потока составляет более 2 000 км/ч, что почти в 2 раза превышает скорость звука. А температура достигает 10 000°С, для сравнения температура на поверхности Солнца равна 6 000° по Цельсию.
Самыми важными узлами в установке плазменной резки являются:
- Источник плазменной резки;
- Горелка;
- Система автоматического контроля и управления высотой горелки (THC);
- Рабочий стол;
- Система управления станком.
Источник плазменной резки
Самым важным этапом при выборе установки является выбор источника плазменной резки. В наше время существует множество производителей таких источников с разными характеристиками и показателями по эксплуатации. Есть дорогие импортные источники, которые хорошо зарекомендовали себя при работе в «российских» условиях, и есть отечественные, цены на которые гораздо ниже.При выборе источника покупатель смотрит на технические характеристики максимального значения толщины разрезаемого металла, при этом зачастую он не обращает внимание ни на тип металла, ни на способ резки. Эта опрометчивость приводит к тому, что источник не выдает указанных характеристик при работе. Например, установка с максимальной толщиной разрезаемого металла 40 мм не может прорезать заготовку толщиной 40 мм. Производителя нельзя винить в обмане покупателя, так как данный расчет произведен на углеродистую сталь с идеальной подачей электроэнергии и достаточное давление газа. Следует учитывать и знать то, что в технической документации значения всегда максимальны, т.е. это все, на что способно данное оборудование, но это не значит, что аппарат будет постоянно работать в таком режиме. Если вы преимущественно производите раскрой металла толщиной до 20 мм, то вам необходимо приобретать аппарат, который режет толщины не менее 38-40 мм. На пробой такой аппарат прорежет максимум 16-18 мм.
Пример максимальных характеристик для источников плазмы одного из популярных в России производителей приведены в таблице 1.
Таблица 1. Максимальные характеристики для источников плазмы.
Характеристика |
Единица измерения | Источник на 130А | Источник на 260А | Источник на 400А |
Максимальная производительность резки при высоком качестве (MS) (кромки) | мм | 38 | 64 | 80 |
Максимальная производительность резки при высоком качестве (MS) (прожига) | мм | 16 | 38 | 50 |
Максимальная скорость позиционирования X / Y | м/мин | 35 | 35 | 35 |
Максимальная скорость резки | м/мин | 12 | 12 | 12 |
Точность позиционирования | мм | +/-0,1 | +/-0,1 | +/-0,1 |
Повторяемость | мм | 0,1 | 0,1 | 0,1 |
Выходной ток | А | 130 | 260 | 400 |
Текущий диапазон регулирования | А | 30-130 | 30-260 | 30-400 |
Горелка
Рис. 1. Схема горелки
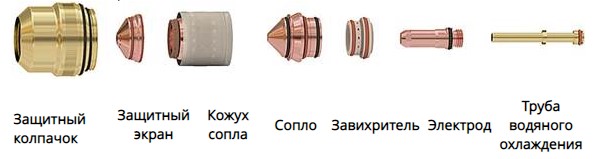
На рис. 1 представлена схема горелки, самой эксплуатируемой части плазменного станка. Чаще всего замене подлежат сопло и электрод. Их износ оказывает значительное влияние на качество резки. Самые популярные причины выхода горелки из строя, помимо естественного износа, являются низкая квалификация оператора, большая влажность воздуха, частое использование интенсивных режимов.
При выборе станка обращайте внимание на скорость поставки запасных частей. Использование оригинальных деталей от производителя продлит срок службы установке.
Система автоматического контроля и управления высотой горелки (THC)
Современные технологии плазменной резки делают обязательным использование системы контроля высоты горелки. Производители установок плазменной резки гарантируют качество реза на заявленных толщинах только при наличии такой системы.
Эта система предназначена для управления приводом опускания и поднятия горелки в процессе плазменной резки металлов. Устройство обеспечивает работу машины в автоматическом и ручном режиме с использованием одного или двух лифтовых устройств. Система оснащена выносной графической панелью, позволяющей производить корректировку параметров и режимов работы.
Система использует напряжение дуги плазмы, чтобы управлять физической величиной высоты, расстоянием между резаком и обрабатываемой деталью в течение процесса плазменной резки. Метод обнаружения поверхности достигается контактным сенсором плазменного резака или ограничением силы столкновения резака с обрабатываемой поверхностью.
Сам стол для машин плазменной резки представляет собой жесткую конструкцию, предназначенную для укладки листов толщиной до 200 мм.
В нижней части расположена система удаления дыма и частиц металла. Она состоит из секций размером примерно 500*500 мм, каждая секция может работать автономно, то есть при резке удаление отходов происходит только под задействованной в резке секцией. Такие установки наиболее энергоэффективны.
При резке плазмой на больших токах выделяется очень много металлической аэрозоли, которая впоследствии превращается в металлический абразив. Поэтому узлы стола рассчитаны работать в очень жестких условиях. В столах используется специальная пылезащищенная пневматика. Все узлы легкодоступны, поэтому в случае необходимости их легко заменить. Столы шириной от 2,5 метров имеют каналы для дымоудаления с двух сторон.
Рабочая поверхность стола чаще всего изготовлена из стальных пластин. Расстояние между пластинами бывает разное, его нужно выбирать исходя из размеров деталей, которые вы планируете вырезать, чтобы они не проваливались. Дополнительные пластины вы всегда сможете нарезать на самой установке. Обычно завод-изготовитель бесплатно поставляет программу раскроя таких пластин.
Рис. 2. Схема рабочего стола плазменной установки
Чаще всего рабочий стол бывает двух типов:
- Рабочий стол интегрирован с координатной системой.
- Рабочий стол и координатная система расположены на разных фундаментах.
Выбор конструкции установки обусловлен ограничениями по производственным площадям и максимальной толщиной металла, который планируется резать. Для металла до 10 мм подходит первый вариант, потому что он занимает меньше площади на производстве. Если же толщина металла более 10 мм, то целесообразным будет выбор второго варианта. Дело в том, что при резке больших толщин стол нагревается и со временем деформируется. Поэтому лучше будет, если направляющие будут смонтированы отдельно от рабочего стола. Типовые размеры рабочего стола обычно имеют следующую классификацию: 1500x3000 мм, 2000х6000 мм, 2000х12000 мм. Конечно, размеры стола могут быть и другими, но это уже нужно уточнять у завода-изготовителя.
При подборе плазменного станка оцените удобство и качество ЧПУ. Не секрет, что благодаря системе ЧПУ достигается высочайшее качество резки.
При помощи ЧПУ машина плазменной резки точно согласовывает перемещения горелки и работу источника плазмы, включая, в том числе, и управление подачей газа. Благодаря тотальному контролю с ЧПУ и обширной обратной связи машина плазменной резки может точно, а главное, заблаговременно диагностировать события, которые могут привести к сбою в работе или поломке. В этих случаях машина выдает информацию об ошибках или, если необходимо, блокирует неправильные команды/работу.
Сенсорный экран с большой диагональю, понятный, продуманный интерфейс – все это делает машину не только эффективной, но и эргономичной, понятной и удобной в эксплуатации. И, конечно, лучше выбирать систему ЧПУ со встроенным модемом, чтобы специалисты сервисной службы поставщика могли удаленно посмотреть ошибки и изменить машинные параметры.
Специальное программное обеспечение предназначено для создания карт раскроя и вывода управляющих программ для станков плазменной резки. Такое ПО позволяет выполнить оптимальную укладку необходимых деталей на лист в автоматическом или ручном режиме, произвести расчет необходимого материала, рассчитать время, необходимое на обработку, выводить различные технологические и экономические отчеты, связанные с расчетом стоимости деталей, коэффициента использования листового металлопроката и т.д. Существует огромное число различных программ, но выбирать нужно ту, которая обладает удобным интерфейсом, с корректным русским переводом и в полной мере соответствует вашим критериям по функциональности.
Я рекомендую такие программы, как PRONEST, LANTEK или METALIX.
Опросник для подбора установки плазменной резки
Мы рассмотрели основные узлы плазменных машин и особенности, которые нужно учитывать при подборе данного вида оборудования. В заключении я представляю вашему вниманию краткий список вопросов, ответ на которые поможет вам подобрать оптимальный для вас станок:
- Какой тип металла вы будете раскраивать?
- Какова минимальная и максимальная толщина резки?
- На какой максимальной толщине вам необходима врезка (прошивка)?
- Какие требования к чистоте и точности реза?
- Нужно ли вырезать окружность, диаметр которой равен или меньше толщины листа?
- Нужно ли осуществлять рез под углом?
- Какой размер листа вы планируете резать?
- Сколько часов в сутки планируется эксплуатировать установку?
- Какое количество деталей необходимо раскраивать в смену/месяц/год?
- Какие есть ограничения по производственным площадям?
- Какие есть ограничения по электрической сети?
- На какой бюджет вы рассчитываете?